The Process of Applying Teflon Spray Coating
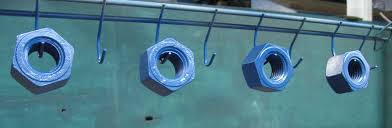
When one mentions the term “nonstick”, the name “Teflon” is very likely to pop up. Teflon’s applications – and its nonstick properties – are responsible for its popularity in the modern world. While a lot has been said and heard about Teflon the brand, how much do you know about the Teflon coating process? Chances are, not much. To begin with, Teflon is the shortened form, and the trade name, used for the mainstay material known as polytetrafluoroethylene (PTFE). It is essentially a plastic-type (fluoropolymers) that is composed of tetrafluoroethylene molecules (TFE). Further to the nonstick feature, a Teflon spray coating equips implements with many features. Meanwhile, what makes Teflon coatings a hot favorite is its compatibility with other materials. PTFE works well on materials such as steel, brass aluminum, glass, fiberglass, types of rubber, plastics, and magnesium. Considering Teflon’s dynamicity, we thought it would be interesting to walk you through the behind-the-scenes of the spray coating process.
The first step entails the preparation of the surface on which the Teflon coating is to be sprayed onto. The surface needs to compatible with the Teflon coating to be applied evenly. A well-suited surface ensures that the coating is sturdy and smooth, and assists in improving the shelf-life and service of the coated item. Thus, at the very onset, the grit blasting procedure is applied. It is a process wherein high-pressure steam containing grit particles is applied onto the surface of the item to be coated. Grit blasting is essentially deployed to eliminate any contaminants whatsoever on the object’s surface. The high-pressure stream is an important ingredient in the scheme of things because it contains specific abrasive materials that improve the overall texture of the object’s surface. It must be noted that different types of grit particles are used in the blasting process; depending on the thickness of the coating and its purpose. Typically, aluminum oxide is one of the standard materials used in the grit blasting process, but there are several other choices to choose from. The level of roughness decides the ease with which the Teflon coating will get attached to the surface. The rougher the surface, the more easily the Teflon coating will attach itself. To create evenness on the surface, bonding agents such as resin is used to enable Teflon to stick easily and firmly onto the surface. Once the surface is readied, the Teflon coating can be applied. The two application methods frequently used are conventional coating and electrostatic coating. The choice of method is determined by the equipment available and the thickness of the coating you want.
In conventional spraying, compressed air is used to assist in the paint application task. The coating paint is inserted in a spray gun. Then it is held at a perpendicular angle to the surface, and the spray is applied in rectangular motions. Held in trained hands, the spray gun dispenses the coat in small liquid droplets, and it is evenly applied on the surface. If done right, the outcome is a coat with a uniform and glossy finish. The conventional method is resorted to most often for it doesn’t demand any special tools to be used. As a result, the method is cost-effectively, and especially suitable for items that have out-of-the-ordinary designs, shapes, and surfaces. A compulsory pointer to keep in mind is that the spray gun should not have a filter as the air-lines will be uneven, resulting in mediocre Teflon coating.
Electrostatic coating is ideal when there are large quantities of items or equipment that need a Teflon coating. The electrostatic coating method is the same as the conventional coating in terms of application. The only point of difference being, the spray guns are modified, and they require skillful handling. These guns deliver speedy coating and better finishes. Modified guns have an electrode and a tip from which the liquid droplets are released. As the droplets are negatively-charged, they tend to stick better on the surface. The tip on the modified gun ensures more precision hence there is no wastage. The electrostatic coating requires users to wear safety gear.
With the Teflon spray coating process laid out for you, we should also inform you about some of the factors that make Teflon such a specialty material in industries. On one hand, Teflon has a very high melting point; it is also true the Teflon material demonstrates significant stability at low temperatures. Applying a Teflon coating on industrial implements ensures they become corrosion-resistant. Another upside of Teflon coating that it doesn’t react to or with water. Due to the high electronegativity of fluorine, Teflon-coated materials do not get wet. Furthermore, Teflon coating endows surfaces to develop the lowest friction. As a result, the coating is very slippery, and therefore an ideal fit for machine components. Teflon-coated machine parts can easily withstand friction, extreme heat, and wear and tear. Teflon coating enjoys widespread usage. From cookware, utensils, nonstick pans and pots, reactors, laboratory equipment, fabrics, carpets, outdoor signs, catheters, vascular grafts, to insulating cables, and much else. Teflon coating is available in paint as well as in powder form. It is applied in the manufacturing process of running shoes. The low friction trait of the Teflon coating allows the shoes to be smooth and comfortable inside out. The result of, users do not experience pain or get blisters on their feet after use.
I wanted to thank you for this great Information and knowledge, I definitely loved every little bit of it. I have you bookmarked your web site to check out the latest stuff you post. Your blog is eye-catching. I get pleasure from it. Thanks for sharing this beautiful piece of writing with me, get more information at Silver Plating Company for more Astfinishing.com related information and knowledge.
ReplyDelete