The Various Benefits of Teflon Industrial Coatings
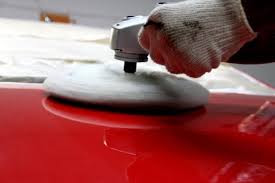
Nonstick Properties: Undoubtedly, the first thing that comes to mind when one hears Teflon is its nonstick trait that is to be found in all its products. One of the big reasons behind Teflon’s popularity as a brand and material is the fact that it does not let things stick to it. The PTFE coating has inbuilt nonstick properties that ensure easy removal and cleaning. PTFE is competent in making sure that hot and cold substances do not permanently attach themselves to Teflon-coated surfaces. This USP feature is the mainstay behind Teflon’s widespread use and success in industrial processes such as moulding, heat sealing, packaging, and much more.
Low Friction and Abrasion Resistant: Teflon coatings are the best bet for industrial use as they guarantee resistance to abrasion and low friction. As a result, when oily or greasy substances are applied on Teflon-coated surfaces (at extremely elevated temperatures), the liquids tend to vaporize, and the Teflon surfaces remain intact. This particular trait has made PTFE’s usage effective for bearing surfaces, shafts, fasteners, stud bolts, and moving mechanisms. Teflon coating’s abrasion-resistant feature enables it to give longevity to applications; you can use Teflon coatings with fillers with a base layer that has been metal-sprayed.
Withstand Extreme Temperatures: Teflon’s usefulness is popular in industries because it can endure extreme temperatures – hold and cold. The primary infrastructure of PTFE is such that it has resistance to most internal and external agents including chemical and fiction. Expanding on Teflon’s trait of tolerating extreme temperatures, this specific quality is what has made Teflon a must-use component in the aerospace industry. Considering that airplanes and aircraft need to be able to tolerate extremely cold conditions at high altitudes, as well as bear with extreme heat from internal agents (placed inside high-voltage equipment), therefore availability and use of Teflon coatings act as a protective gear, and allows airplanes and aircraft to function smoothly, and with maximum safety.
Improves Performance: Teflon coating is credited for improving the performance of machines and equipment. Take automotive parts as an example. They are commonly coated with Teflon for it plays a critical role in making sure that automotive parts function well, and do not suffer from wear and tear caused by extreme use. As it is, when automotive parts experience increased friction and strain, there is bound to be a decline in performance. To steer clear of incurring overhead costs – maintenance, repair, and replacement, the use of Teflon coating is a must.
Anti-Corrosion: Manufacturing sites use various chemicals. Teflon coating is abundantly used in chemical manufacturing facilities. Manufacturing units wherein volatile compounds and substances, and raw materials on used daily, the use of Teflon coatings is popular for they endow manufacturing equipment with anti-corrosion properties. Furthermore, Teflon coatings stand out because they create a protective and durable shield that safeguards manufacturing machinery against wear and tear caused by chemicals; critical manufacturing parts are prone to get affected. As is the case in other industries, the application of Teflon coating prevents manufacturing equipment from experiencing functionality and performance issues that arise from corrosion.
Anti-Contamination: Among the many plusses that make Teflon a widely-used coating substance is its ability to act as an anti-contaminant. No prizes for guessing then that Teflon coating is routinely used in food, biomedical, and related industries. As part of the FDA rules and regulations, companies need to ensure that they deploy components and equipment that mitigate the risk of contamination in sensitive supplies. Fortunately, Teflon coatings are highly skilled and useful in this context. Teflon coating is equipped with agents that give it anti-bacterial and anti-contamination properties. The result of, microbes, bacteria, and other harmful contaminants do not play spoilsport in the manufacturing and production of food items and biomedical consumables. In the case of the latter especially, Teflon coating is used on medical devices that are to be placed inside patients.
As can be seen, Teflon has an assortment of benefits in its composition and character as a result of which it continues to impact the quality and usefulness of goods it is a part of. Whatever industry you may belong to, the use of Teflon is guaranteed. If you need any assistance in procuring top-quality Teflon coating for your supplies, reach out to us today!
Comments
Post a Comment